How can I Calibrate Flue Gas Analyser with Honeywell | City Tech Gas Sensors?
Calibrating a flue gas analyzer is a crucial step to ensure accurate and reliable measurements of combustion gases in various applications, such as industrial processes, heating systems, and environmental monitoring. Here's a general guide to calibrating a flue gas analyzer:
Note: The exact calibration process can vary based on the manufacturer and model of your flue gas analyzer. Always refer to the manufacturer's manual for specific instructions.
Materials Needed:
- Flue gas analyzer
- Calibration gases (usually certified standard gases of known composition)
- Gas regulator (if not included with the analyzer)
- Calibration adapter or probe
- Clean, dry cloth
- Screwdriver (if needed for adjustments)
Steps to Calibrate:
Prepare the Analyzer:
- Make sure the analyzer is clean and free from any debris or contaminants.
- Ensure the battery is fully charged or connected to a power source.
- Turn on the analyzer and let it warm up as recommended by the manufacturer (usually a few minutes).
Select Calibration Gases:
- Check the manufacturer's specifications to determine the appropriate calibration gases and concentrations required for your specific analyzer.
- Calibration gases typically include specific concentrations of oxygen (O2), carbon monoxide (CO), and other relevant gases.
Set Up the Analyzer:
- Attach the calibration adapter or probe to the flue gas outlet of the equipment you're testing.
- If your analyzer has a built-in pump, ensure it's properly connected and functioning.
Connect Gas Regulator:
- If your analyzer requires a gas regulator to control the flow of calibration gases, attach the regulator to the calibration gas cylinder.
Calibration Process:
- Follow the manufacturer's instructions to enter calibration mode on the analyzer.
- Start with zero/span calibration: Use a calibration gas with a known concentration of one of the gases (e.g., zero for O2 or clean air), and adjust the analyzer to read this value as the baseline.
- Follow the same process for span calibration, using a calibration gas with a known concentration of another gas (e.g., CO).
- Some analyzers might require you to manually adjust settings, while others might have an automated calibration process.
Validation:
- After calibration, validate the readings using a certified calibration gas that falls within the range of your analyzer's measurements. This ensures that your analyzer is accurately calibrated across its full range.
Adjustments (if necessary):
- If the readings are not accurate, your analyzer might have calibration adjustment features. Follow the manufacturer's guidelines to make adjustments as needed.
Documentation:
- Keep a record of the calibration process, including the date, calibration gases used, concentrations, and any adjustments made.
Regular Maintenance:
- Calibrate your analyzer regularly according to the manufacturer's recommendations.
- Keep the analyzer clean and properly stored when not in use.
Remember, proper calibration is essential for accurate measurements. If you're unsure about any step of the process, consult the user manual provided by the manufacturer or contact their customer support for assistance.
Gas sensors are crucial components of flue gas analyzers because they are responsible for detecting and measuring the concentration of various gases present in the flue gas emissions. These gases include oxygen (O2), carbon monoxide (CO), carbon dioxide (CO2), sulfur dioxide (SO2), nitrogen oxides (NOx), and more.
Best-selling Honeywell | City-Tech Industrial Gas Sensors:
Here's why gas sensors are so important for flue gas analyzers:
Accurate Measurement: Gas sensors provide accurate and real-time measurements of gas concentrations in the flue gases. This information is essential for understanding the combustion efficiency, emissions levels, and overall performance of combustion processes.
Regulatory Compliance: Many industries and processes are subject to strict environmental regulations that dictate the allowable levels of certain gases in flue gas emissions. Gas sensors help ensure compliance by providing accurate data on emissions, allowing operators to take corrective actions if necessary.
Safety: Some combustion gases, such as carbon monoxide (CO), can be harmful or even fatal in high concentrations. Gas sensors help monitor these gases, providing early warnings if dangerous levels are detected, and enabling operators to take immediate actions to protect personnel and equipment.
Efficiency Optimization: By measuring gas concentrations, flue gas analyzers with gas sensors allow operators to fine-tune combustion processes for optimal efficiency. This can lead to reduced fuel consumption, lower emissions, and cost savings.
Process Control: Gas sensors provide valuable data for controlling combustion processes. By monitoring oxygen levels, for example, operators can adjust air-to-fuel ratios to achieve complete combustion and minimize the production of pollutants.
Data Collection and Analysis: Gas sensor data is often used for data logging and analysis. Over time, this data can provide insights into the performance of equipment, the effectiveness of emissions control strategies, and the need for maintenance.
Emissions Monitoring: Continuous emissions monitoring is critical in various industries, such as power generation, industrial manufacturing, and heating systems. Gas sensors enable real-time monitoring of emissions, helping operators maintain compliance with emissions limits.
Environmental Impact: Flue gas emissions can have significant environmental impacts, contributing to air quality issues and climate change. Gas sensors play a role in monitoring and mitigating these impacts by providing accurate data that can inform emission reduction strategies.
Research and Development: Gas sensors are essential tools in research and development efforts aimed at improving combustion efficiency, reducing emissions, and developing new technologies for cleaner energy production.
In summary, gas sensors are the heart of flue gas analyzers, providing critical information that helps industries and processes operate more efficiently, safely, and in compliance with environmental regulations. They enable real-time monitoring, control, and optimization of combustion processes, contributing to both environmental protection and economic benefits.
Honeywell Gas Analysis Equipments
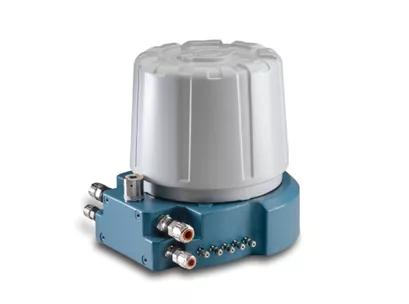
Encal 3000
In natural gas energy measurement, calorific value is a key component that determines the energy content flowing through a pipeline, along with volume, pressure, and temperature measurements. EnCal 3000 helps gas transmission & distribution companies as well as end-users consuming large amounts of gas accurately measure of single gas components since wrong measurements can directly impact the bottom line.
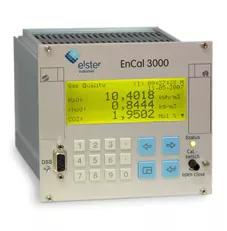
Encal 3000 Controller
The EnCal 3000 controller is available as an option to the gas chromatograph. Besides displaying the incoming data from the EnCal 3000, it offers additional I/O connections like analogue signal outputs, digital contacts and serial connections. For metrological systems subject to PTB approval, the unit provides two years’ data storage for two streams. The control unit can communicate with the EnCal 3000 via TCP/IP or via an RS485 serial interface. The unit is 24 V DC powered and is suitable for installation in a safe area.
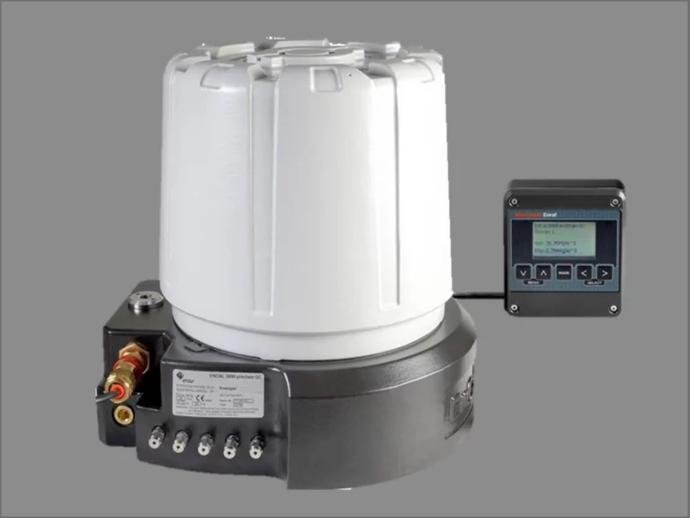
Encal 3000 prochain
The EnCal 3000 proChain is a gas chromatograph specially designed to measure the gas quality of natural gas. It provides the Heating Value and composition. It is certified and can be used for custody transfer.
EnCal 3000 analyzer injects natural gas into a carrier gas stream that further proceeds to a column where natural gas is separated into its constituents. The separated constituents then pass a calibrated detector in peaks and the area of these peaks is dependent on the constituent’s concentrations. With collated data from the constituent’s concentrations, the heating value / Wobbe-index / density of the natural gas is calculated.
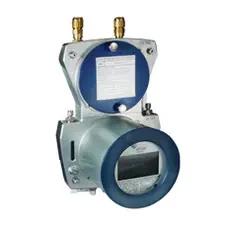
GasLab Q2
As opposed to the 'classic' gas chromatograph solution, the Honeywell Elster GasLab Q2 does not use carrier and mixed calibration gases or combustion air supply. This translates into lower cost of ownership for the user.
- Determination of main gas parameters: calorific value/Wobbe index/density/ CO2 concentration/methane number, etc.
- Flameless: no air or carrier gas needed
- Fast, continuous measurement
- Easy operation
- Small footprint: Low investment and maintenance costs.
Need help?
Don't hesitate to email us sales@spantech.co.uk if you need assistance.